United Fireclay Products, Atlas Brickworks, Armadale, West Lothian.
Alternative brickworks include:
To be read in conjunction with the page for the West Works, Armadale.
Info – www.armadale.org.uk – United Fireclay Products, Etna Works. Armadale, Bathgate, West Lothian, EH48 2JU – a member of the Gibbons Dudley Group producing firebricks and shapes, high alumina bricks made of carbonaceous shale by stiff-plastic pressing. Fireclays are obtained from mines near the plant, crushed by rollers and ground in 11ft diameter pan mills. screened and pressed in stiff-plastic toggle, impact. or hydraulic presses. They are fired in either the tunnel kiln or the shuttle kiln, both natural gas-fired. The building brickworks. (Etna Works, Bathville. NS 944679) was formerly a large fireclay works and has two 10-chamber, one 16 chamber, and one 28 chamber continuous kilns. As with Flettons, no additional fuel is needed after the bricks have been brought to red heat because of the natural fuel content of the clay. In 1976 a 90-ft-high shaft kiln was installed to produce pre-fired clay granules for refractory concrete and for blending with the raw fireclay. It is the largest of its kind in the United Kingdom. Source
********************
John Watson of Glasgow bought the Bathville site in June 1859 for £10, 000 and shortly after built a brickworks to use the fireclay being mined with the coal. John Watson & Co were to become one of the biggest coal masters in Lanarkshire, but in 1874 they ran into financial trouble and the Bathville works were sold to James Wood, another coal master. James and William Wood formed James Wood Ltd in 1893 to take over their interests in Drumpellier, Westrigg, Neilston and Meiklehill Collieries, together with the Bathville Brickworks. Financial trouble in 1895 resulted in James and William Wood having their estates sequestrated, however, James Wood recovered and in 1897 joined Daniel Robertson, a firebrick maker at Bathgate, to incorporate Robertson, Love & Co Ltd., with a capital of £6,000.
A sales catalogue of about 1900 shows a picture of the Bathville Brick and Fireclay Works with 2 substantial groups of buildings served by 4 railway sidings. 6 large and 4 smaller chimneys draw the gases from several beehive kilns and 3 continuous Hoffmann kilns. A wide range of firebricks, sewage pipes and decorated chimney pots are shown.
United Collieries Ltd was formed in 1898 to amalgamate 9 collieries and a further 23 collieries were added in 1902, among which was James Wood Ltd with Robertson, Love & Co brickworks subsidiary. The capital of the group was £2 million, a very large sum. Among the companies amalgamated was the Glasgow Iron and Steel Company of Clydesdale and Calderbank, who after the nationalisation of their steel interests were to become one of the largest brickmakers in Scotland in the 1980s.
Robertson, Love & Co were liquidated in 1916 but continued to make firebricks as part of United Collieries Ltd. When coal was nationalised in 1947, the brickworks were reorganised as United Fireclay Products Ltd. and comprised the Etna and Atlas Firebrick Works, the Bathville Pipe Works, the UNICOL Tile Works, all at Armadale and the Brownhill building brick works at Clelland, Lanarkshire. The chief refractory brands were Etna 933% alumina), Atlas (38% alumina), and Atlas A (42% alumina), all based on local fire clays. The Bents Mine near Stoneyburn supplied an excellent 42% alumina fireclay from which the Mars brand was made, but the fireclay was worked out and the mine closed in 1929. The Drum Mine near East Whitburn took over and the Northrigg No 7 pit supplied fireclay for pipes and some coal. The Tippethill Mine (38% alumina, 2.5% iron) replaced the Drum Mine in 1960 and the Pottishaw Mine replaced Northrigg in 1963.
Woodall – Duckham bought United Fireclay Products Ltd in 1957 to secure their source of fireclay shapes for gas retorts. The modern West Works was started in 1960 with a 400-foot tunnel kiln. Heathfield & Cardowan Pipeworks Ltd was bought in 1968 and at that time the Company was at its largest capacity, employing about 600 men and women. Demand for pipes fell due to competition from plastic pipes and the Bathville Pipe Works was closed in 1970. Lower demand for refractories led to the Etna works being converted to make building bricks under the Etna brand and the closure of the Atlas Works in 1973. The Company had again changed hands being bought by the Gibbons Dudley Ltd for £715,000 in March 1971. As refractory demand fell further the Company was bought by Steetley Ltd in 1981, who changed the West Works into a facing brickworks and sold the Etna and Brownhill Works to GISCOL Ltd.
Before all these changes the Company had earned a high reputation for their firebricks and then high alumina bricks which they developed in the post-war period. James Smith was the managing director during this period with John McWilliam as his technical director. Smith was followed after his death in 1976 by Bill Stickler, then by Graham Pearson. Source The Scottish Refractory Industry 1830 – 1980.
Below – 11/03/1898 – Dundee Courier – The United Collieries Limited incorporated. Share capital £200,000 … The following brickworks were acquired – Ellismuir Brickwork, Ballieston and Wellshot Brickwork, Cambuslang. See the link for the full prospectus.
06/05/1899 – Dundee Advertiser – The first meeting of the shareholders of the United Collieries Company Limited was held at the Merchants Hall, Glasgow yesterday … The directors had found that the manufacture of the bricks at Wellshot was very remunerative and they resolved early in the year on the erection of an additional kiln, which had practically doubled the output which was now about 30,000 bricks daily.
Below – 1900 – Robertson, Love & Co Ltd – Bathville Brick & Fireclay Works, Armadale Station, West Lothian – Catalogue dated c. 1900.
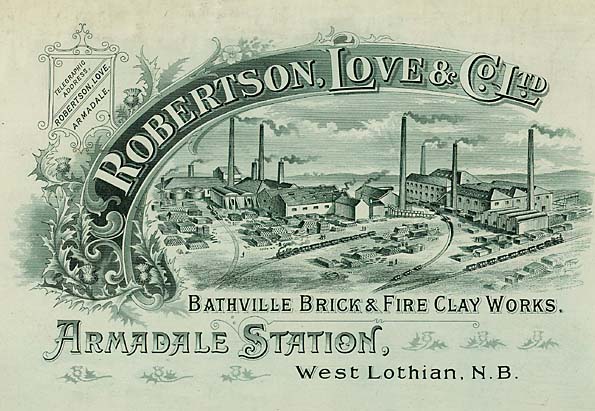
28/07/1902 – The Scotsman – Sale of £1,000,000 five per cent first mortgage debentures of the United Collieries Limited. The company comprises an amalgamation of colliery properties in Lanarkshire and other counties in Scotland and includes:-
Armadale Coal Co Ltd, Collieries and Brickworks
William Black and Sons Ltd, Collieries and Brickworks
Cambuslang Coal Co Ltd, Collieries and Brickworks
Loganlea Coal Co Ltd, Collieries and Brickworks
Morningside Coal Co Ltd, Collieries, Fireclay and Brickworks
John Nimmo and Son Ltd, Collieries and Brickworks
United Collieries Ltd, Collieries and Brickworks
James Wood Ltd, Fireclay and Brickworks
04/02/1903 – The Scotsman – There has been lodged the agreement between the Collieries Consolidation Syndicate Limited of Suffolk House, Cannon Street, London and the United Collieries Limited, Glasgow, for the purchase by the latter of certain collieries in Lanarkshire and leases of coalfields, fire clay and brickwork sand railway waggons at £2,444,945 …
26/07/1907 – Motherwell Times – Man wanted as Panman for Bradley and Craven brick machine; wages 4s per shift. Apply Manager, United Collieries Brickwork, Carfin.
31/07/1917 – Daily Record – The death was reported yesterday of Mr John F Baird, Edgehill, Castlehead, Paisley who was well known in Glasgow and local business circles and had been for a time a director of the United Collieries Company, the Kelvinside Brick Company, the Cleghorn Terracotta Company Limited besides having been managing director at Speirs, Gibb & Company’s Paisley works and for a period chairman of Messrs McGee Ltd, Engineers. He was a member of the Parish Council and for a period chairman.
Below – 10/06/1933 – The Scotsman – James Wood dies.

1936 – 1937 – United Collieries Ltd. Colliery proprietors, coke and char makers, brick (fireclay, red, and composition) and tile manufacturers, 109 Hope st. C.2. Telephone, Central 6700; tel. address, “Combined, Glasgow.”
1939 – 1940 – William Leckie, Brick Salesman, United Collieries Ltd. Ho Dunedin, Croftbank Crescent, Uddingston.
27/05/1939 – Airdrie and Coatbridge Advertiser – … The other new industry is that of fire clay mining, about a mile from the factory. It is understood that United Collieries Company, Ltd., is to sink a surface shaft for the purpose of working a valuable seam of fireclay. As the result of a recent bore to test the strata at this point, the fireclay seam has been located, and there is every indication that it can be economically worked. Brick-making operations in several districts of Lanarkshire have been restricted owing to a lack of materials. It is believed that the clay will be suitable for the manufacture of fireclay bricks and also for pipes, which require special clay for the purpose. Boring operations for coal are also being carried out by the company in the Newarthill, Newhouse, and Cleland districts. It is understood that the result of the bore is favourable to the project of sinking a new pit in this district, as there are several seams of coal capable of being economically worked …
1941 – 1942 – United Collieries Limited, Bathville Brickworks, brick, pipe and tile makers.
29/03/1946 – West Lothian Courier – Death of Mr John Finlay, managing director of United Collieries Ltd. The death occurred at his residence Wyndwood, 38 Glasgow Road, Uddingston on Tuesday of Mr John Finlay, managing director of the United Collieries, Ltd. Mr Finlay had been indisposed for two or three months over the new year period but recovered sufficiently to enable him to return to business a few weeks ago. He visited the offices and works of the company at Bathville as recently as last Thursday but became ill again and in the end, his death came somewhat suddenly. A native of Law, Lanarkshire Mr Finlay started work as a pit bo in the district and from the first, he showed himself to be of a studious disposition. As a result, he steadily worked his way up until he became manager of Kingshill Colliery, owned by the Coltness Iron Coy., Ltd. Later he was appointed manager of the Edinburgh Collieries, Ltd, a position which he held for nearly ten years. Mr Finlay joined the United Collieries, Ltd., as general manager, in 1927, and ten years later became managing director of the Company. A past president of the Mining Institute of Scotland and a representative on the Council of the Institution of Mining Engineers, he was a well-known figure in the coal trade and was regarded as one of the leading personalities in the industry in Scotland. Mr Finlay was also well versed in the pipe and brick-making industry, and only a short time ago he launched a new scheme for tile making. Under his direction, a new work was built at Bathville, Armadale for the making of glazed tiles and slab fireplaces and it is a tragic circumstance that he has not been spared to see in full production a venture which was a striking example of his initiative and enterprise. Lately, he was also instrumental in the taking over, by the Company, of a drain tile work at Auchenheath, Lesmahagow. Actively concerned in various branches of the industry to the very end, Mr Finlay took a deep interest in and was a source of much encouragement to young mining students who sought to pursue the study of the science of mining and to them his own experience was of invaluable assistance. He was deeply interested, too, in the welfare schemes associated with the industry, while the interest he also manifested in the activities of other social organisations was recognised by his appointment, by several of them. as honorary president. A keen sportsman, Mr Finlay’s favourite pastime was golf. He also interested himself in football, with Celtic F.C. as his favourite club. He had a wide circle of business associates and friends who held him in high regard. He paid frequent visits to the Company’s offices at Bathville and was highly respected in the Armadale district. For several years, Mr and Mrs Finlay with their family, resided at Bedlormie House, near Blackridge, but took up residence in Uddingston some years ago. He was 60 years of age and is survived by his wife. a son (Dr Finlay) and four daughters, to whom deep sympathy has been extended in their bereavement.
01/07/1948 – Birmingham Daily Post – United Fireclay Products Ltd., was incorporated to take over from The United Collieries Ltd.
11/08/1950 – West Lothian Courier – Engineer fitter required for a group of brickworks. Experience of brickworks is desirable but not essential. Good rate of wages paid. Apply to United Fireclay Products. Ltd, Bathville Office, Armadale.
25/04/1952 – West Lothian Courier – Capper’s right of way dispute. Matter raised in the House of Commons. A dispute regarding what has always been considered a right-of-way between four tenants of Glenlark House, Cappers, Armadale, and the management of the United Fireclay Products work, which had been the subject of many negotiations between the parties chiefly concerned, reached a climax when the management of United Fireclay Products, Ltd., from whose water and electricity supplies the tenants of Glenlark are served, caused these services to be withdrawn. This action brought the negotiations to a deadlock, and the assistance of the County officials was sought. Mainly through the good offices of Provost James McKeown, who, although the locus of the dispute is outside the Burgh boundary, with the County officials tried, without success, to find a way out of the impasse. Eventually, Provost McKeown placed the matter before Mr John Taylor, M.P. for West Lothian, and on Friday last Mr Taylor asked the Minister of Health in the House of Commons if he was aware that the water supply had been cut off from Glenlark. The result was that the Secretary of State for Scotland intervened and following a visit by a Department of Health official on Monday last, the water supply was restored, although the Coy. maintain that their own supply is inadequate for the needs of the works and houses. The Company, who wish to have their works entirely enclosed, did offer an alternative access to the houses but, as the new roadway would add a considerable distance to the town from Cappers, the tenants turned the suggestion down. It would appear that the road in dispute rune from Tarraseoch Avenue, to where it joins the Batlhville Rd at Duncan’s Entry and has been in use for many years. The matter created a great deal of comment in the district, and as the electricity supply had not been restored at the time of writing, it would seem that the dispute has not yet been resolved.
Below – 19/07/1957 – The Glasgow Herald – United Fireclay results and an offer from Woodall Duckham.
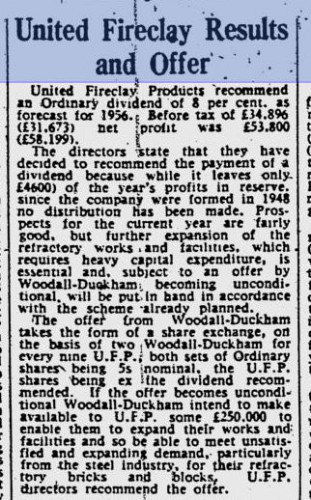
17/01/1958 – West Lothian Courier – Presentation from colleagues. Mr John Haston, formerly assistant to the chief technical engineer at the United Fireclay Products. Ltd, Bathville, who left recently to take up an appointment with the NCB at Ayr, was presented with a Parker fountain pen as a parting gift from the engineering staff. Mr John Weston, chief technical engineer, in making the presentation referred to the efficient manner in which Mr Heston had discharged his duties and extended to him the good wishes of the engineering staff for his future success. Mr Haston suitably acknowledged the gift.
01/07/1958 – Birmingham Daily Post – United Fireclay Products Ltd. As already mentioned, during 1957 the parent company acquired the whole of the shares of United Pireclay Products Limited. This acquisition ensures the certainty of supplies of high-quality firebricks to the group as well as substantial reserves of raw materials from which refractories are made. United fireclay Products Ltd., was incorporated on 1st July 1948, to take over from The United Collieries Ltd., the refractory, salt-glazed pipe and building brick activities carried on by that company as ancillary to its colliery activities after the latter had been nationalised. Since its incorporation the works have been largely modernised, fully £374,000 having been spent on them, including considerable development of the company’s clay mines. Valuable additions have been made to the company’s leases of fireclay and there are, it is estimated, ample reserves of high-class material available to meet any demands in the future. During the past ten years, the company has concentrated its development on the refractory side owing to the considerable increase in the demands by the steel industry, and for some time past it has not been able to meet this growing demand. Many of the large steel companies are amongst its customers for high alumina firebrick supplies which are used by them for special applications. Plans have been initiated therefore for increasing the capacity of this side of the production, particularly looking to the fact that with the gradual diminution of the housing programme the demand for pipes and building bricks is tending to fall off. In conclusion, I would like to offer to all those employed in the various companies making up the Woodall-Duckham Group the warm appreciation of my colleagues and myself for their fine efforts during the past year which have been the main cause of the group’s success. The report and accounts were adopted and the final dividend of 15% less income tax, making 2o% less income tax for the year was approved. The retiring director, Mr J. Simpson, M.lnst Gas E., was re-elected and the remuneration of the auditors. Messrs. Longcroft, Smith & Company was fixed. The resolution amending the articles of the association having been passed, the proceedings terminated.
Below – 29/04/1959 – United Fireclay Products Ltd Railway wagon label – Etna & Atlas Brickworks Armadale to Nottingham. Dated 26/04/1959.

Below – 11/1959 – The Refractories Journal – Woodall-Duckham 11th annual general meeting. This is an extract detailing the UFP.

06/05/1960 – West Lothian Courier – United Fireclay Products Ltd, registered office, 140 West George Street, Glasgow announces the following board changes. Mr J. H. Strathie has been appointed deputy chairman in place of Mr W. G. Logan who has relinquished the deputy chairmanship owing to illness. Mr Michael Richards has resigned from the board. Mr J. H. Johnston has been appointed a director.
Below – 06/1964 – The Refractories Journal – Woodall-Duckham annual general meeting. This is an extract detailing the UFP.
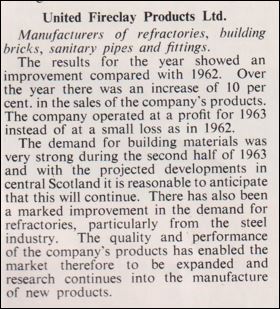
Below – 07/1964 – The Refractories Journal – Product list.
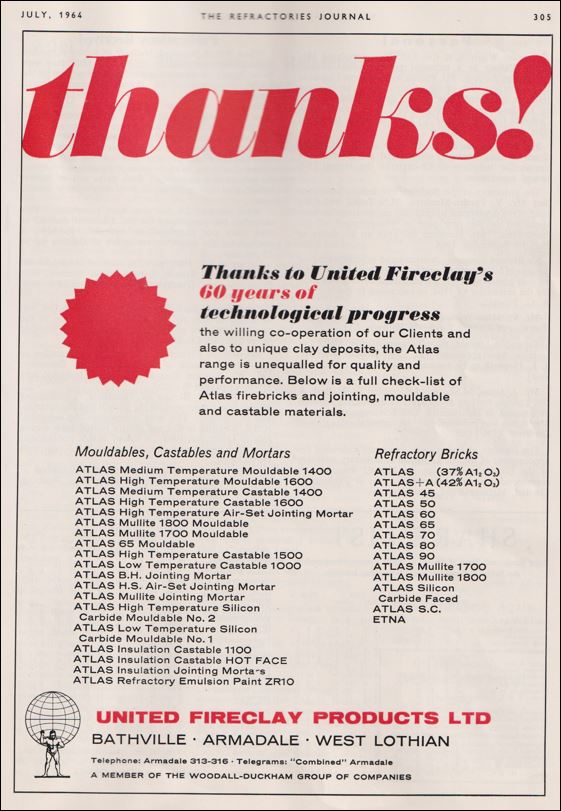
Below – 20/11/1964 – Wishaw Press United Fireclay Products advert with reference to Bathville pipes and fittings, Etna and Brownhill building bricks.
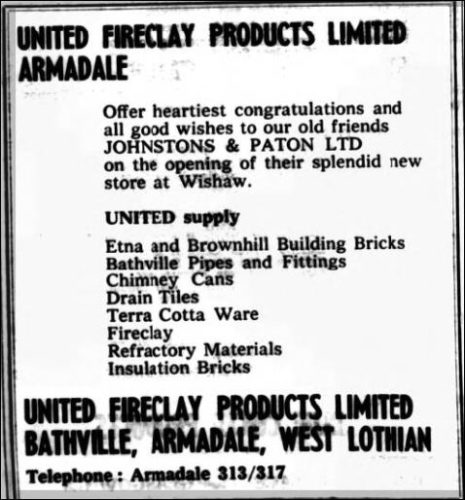
08/01/1965 – West Lothian Courier – Director Appointed United Fireclay Products Ltd, Bathville, Armadale have announced that they have appointed an additional Director as from 1st January 1965 in Mr John Weston, A. M. I. Mech.E. Mr Weston is well known locally having been educated at the Lindsay High School, Bathgate, and later at Heriot-Watt College, Edinburgh. where he was a medallist in engineering. He commenced his apprenticeship as a draughtsman with Dickson & Mann Ltd qualifying in 1939, but his employment with this company was interrupted by war service with the Royal Engineers, He rejoined Dickson & Mann Ltd after the war, attaining the position of works manager. In 1950. Mr Weston was offered and accepted the post of Chief Engineer with United Fireclay Products Ltd, since when he has served with them in this capacity.
Below – 21/05/1965 – West Lothian Courier – United Fireclay Products Ltd. Owing to considerable expansion of production capacity a number of vacancies arise for unskilled operatives to train for semi-skilled jobs on both day and night shift operation … Works manager, Etna Brickworks, Armadale.
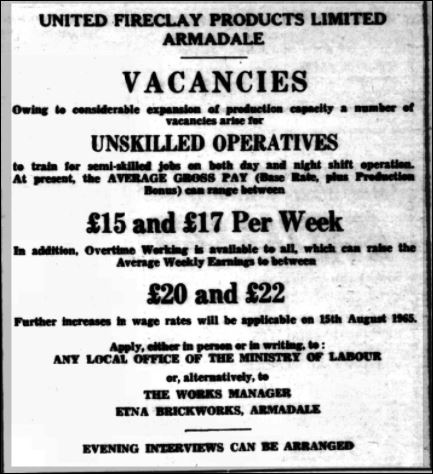
19/08/1966 – Aberdeen Press and Journal – United Fireclay Products Ltd, Armadale, West Lothian. Representative. A vacancy for the position of representative for the above company in the North of Scotland will shortly occur. The position involves mainly selling salt glazed pipes, building bricks and specialities. A fixed salary and car are provided. There is a contributory superannuation scheme and free group life assurance. Candidates should be resident in the general Aberdeen area and should have contact with the building trade, preferably selling the above or similar products. Applications in confidence to the secretary at the above address.
19/05/1967 – West Lothian Courier – Old in years but modern in outlook. At their Bathville Works, United Fireclay Products Ltd, a wholly-owned subsidiary company the Woodall-Duckham Group, produces building bricks, sanitary pipes and a range of refractories and refractory specials for use in a wide range of high-temperature furnaces. At all times it has been the policy of the company to endeavour to meet the ever-changing and more rapidly changing demands in the technological field and to this end, it has well-equipped laboratories to assist with not only the technical control of its product but for research and development purposes.
The production capacity at Armadale in building bricks and pipes is substantial in relation to the total Scottish production of these commodities. The company’s effort in this direction, in terms of bricks produced per annum, is approximately the equivalent of 2500 complete houses and its pipe production, using the same comparison, meets the requirements of 6000 houses per annum. This section represents approximately half of the company’s production.
In contrast to the building materials section, the other half of the company’s activities embrace the very specialised field of high duty refractories and refractory specialities, which products find application in all of the major high-temperature industries throughout the world. Refractory or heating bricks are used as furnace linings in the many and varied industries where high temperatures are required.
At the Armadale Works, refractory is carried out at the Atlas Works, which been established for many years, and at the modern tunnel kiln at the West Works. It will be appreciated the very nature of the business described and the field of distribution calls for a wide variety of skills and training. The company employs approximately 400 operatives and staff and offers scope in a variety of unskilled and semi-skilled jobs in the production of bricks, pipes, refractories, clay mining etc and in addition, offers the opportunity for training in many specialised jobs. It is company policy to encourage promotion in any section of the business from within, if possible, and this policy can enable an employee if he is capable, competent and prepared to take the appropriate training, to obtain progressive advancement and indeed in exceptional cases to top management. Every encouragement is given to young people, and indeed to any employee, to take full advantage of further education, by way of day release or evening classes. There are many interesting, stimulating and challenging posts within the company and prospects are good, but it is not possible, in the limited space available, to describe these adequately. A warm welcome is extended to the individual, or group, to visit Bathville to see for themselves and to have a chat with the management and others concerned in their particular interest.
Below – 19/05/1967 – West Lothian Courier.

06/11/1968 – Birmingham Daily Post – United Fireclay Products Ltd, Bathville, Armadale, West Lothian. Wish to expand their representation in Birmingham, London and South Wales areas. Technical qualification and experience in selling refractory materials including high alumina refractories and mouldables and castables required. Good salary and conditions. Participation in the company’s contributory pension scheme and free life insurance are offered for these positions. Candidates should address their applications to the secretary.
27/06/1969 to 15/05/1970 (numerous adverts) – West Lothian Courier – United Fireclay Products Ltd, Bathville, Armadale, West Lothian. Telegrams ‘combined’ Armadale. Telephone Armadale 671. Require the following: Kiln drawers, kiln setters, brick machine men, mixers, lifters off and general hands. Previous experience is not essential as training will be given. New improved wage scales and night shift allowances in operation giving opportunity for high earnings and advancement within the grades. Overtime working available. Apply either in person or by telephone to the Personnel Officer, Etna Office, Bathville, Armadale.
10/04/1970 – West Lothian Courier – United Fireclay Products Ltd, Bathville, Armadale, West Lothian. Telephone Armadale 671. Require a gatekeeper to be responsible for manning during alternate weeks, the main entrance gates when the works are closed. Gatehouse is available at a nominal rental. Applications should be made to Mr W. Hammond, Bathville Pipeworks manager.
1971 – Gibbons Dudley Group purchases United Fireclay Products.
31/03/1972 – West Lothian Courier – United Fireclay Products Ltd, Armadale, Bathgate, West Lothian. Telephone Armadale 30671. A member of the Gibbons Dudley Group have a vacancy for a purchasing office/stores manager. This medium-sized company with purchases of approximately £600,000 per annum requires a competent purchasing officer to fill this post. Desirably, he should have had experience in all aspects of purchasing, stores control and administration. The company has a contributory superannuation scheme, and group life assurance cover to the extent of 21 years’ salary. Applications, which will be treated in the strictest confidence, should be addressed to the company secretary.
Below – 27/09/1974 – West Lothian Courier – West Lothian Courier – United Fireclay Products Limited require brick operatives at their West Works, Armadale and the Etna Brickworks.
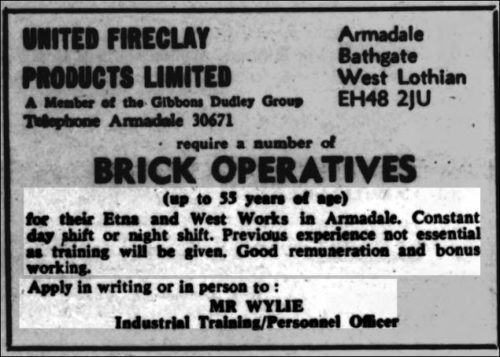
1976 – Brick and Clay Record December – United Fireclay uses shaft calciner to meet refractory raw material needs – High-fired fireclay aggregate for refractory brick and specialities prepared in a shaft calciner. Unit is the largest of its type in the UK. Both refractories and brick are manufactured at the plant site midway between Edinburgh and Glasgow, Scotland.
The use of increasing amounts of grog and pre-fired clays for monolithic refractories and in regular brick production, coupled with improved manufacturing techniques that produce less rejects, has created a higher demand for calcined materials. United Fireclay Products Ltd., a member of the Gibbons Duddley Group, placed a shaft calciner on stream which is considered to be one of the largest and most sophisticated of its type in the UK.
Fireclay is screened and graded at the mine and transported by truck to the kiln, It is elevated to the top and is progressively fired up to 2650F and cools as it falls by gravity down to the bottom discharge. The output of the 90ft high kiln is about o.5 tons per hour.
The production at Armadale, West Lothian location consists of fireclay brick and shapes, high alumina brick, monolithic refractories and building brick. High alumina bricks are made mostly from imported bauxite and calcined flint clay. The materials are crushed, screened and ball-milled as necessary in the high alumina crushing plant. Fireclay bricks and shapes are made mostly from local clays obtained from near the plant using underground mining. These materials are crushed prior to storage, using a roll crusher. Large 11-foot diameter pans and screens are used to size raw material for production. Fine materials are handled in a pneumatic blowing system.
Several types of presses are used in production. Stiff plastic presses, mechanical toggle presses, impact presses and hydraulic presses are all used to manufacture the many sizes and shapes. Double shaft mixers, mulled mixers and a high intensity counter current mixer are used in the various operations prior to pressing.
A tunnel kiln and shuttle kiln using natural gas for a prime fuel are used for firing. Cars are unloaded by forklift, then sorted, palletized and shrink filmed for shipment.
Building bricks are also produced at the plant site. The clay, which contains appreciable carbonaceous material, is pressed by stiff plastic presses and stacked into setting cubes. Lift trucks are used to load the 4 continuous kilns. 2 of the kilns have 10 chambers, 1 has 28 chambers and the other 16 chambers. After ignition, no additional fuel is needed in the process because of the natural fuel in the brick. Unloading also is by lift truck. Shipments are made in both banded packages and loose truckloads to local markets.
Below – 14/11/1977 – United Fireclay Products Ltd headed notepaper. The ‘G’ – stands for Gibbons.
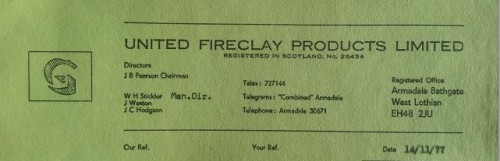
c. 11/1978 – Refractories Journal.
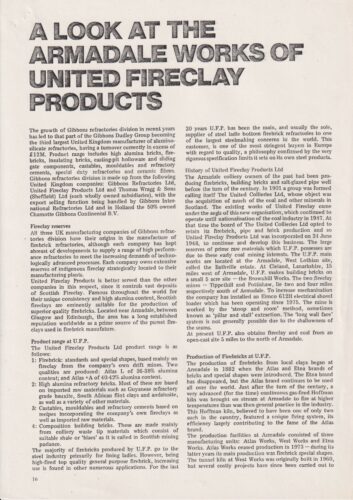
.
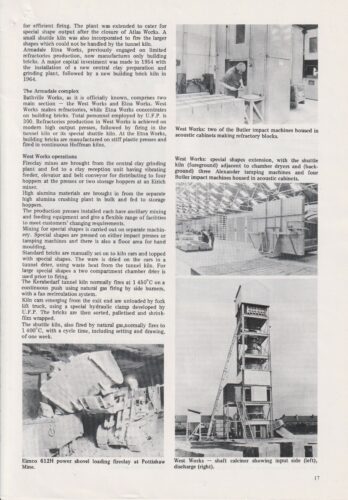
.

.
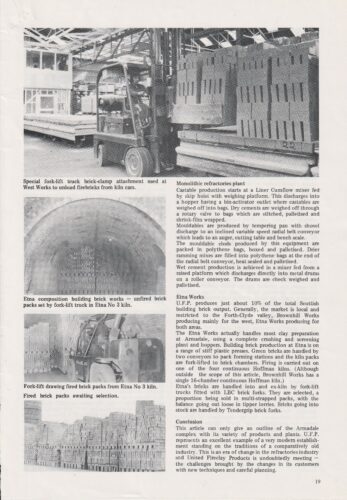
Below – 31/07/1981 – Steetley Letterhead – UFP Works, Armadale.
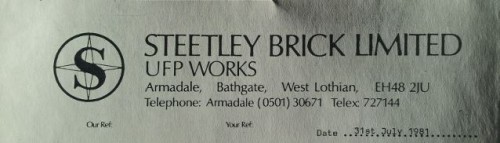
Below – Shaft Calciner – United Fireclay Products Ltd, Armadale.
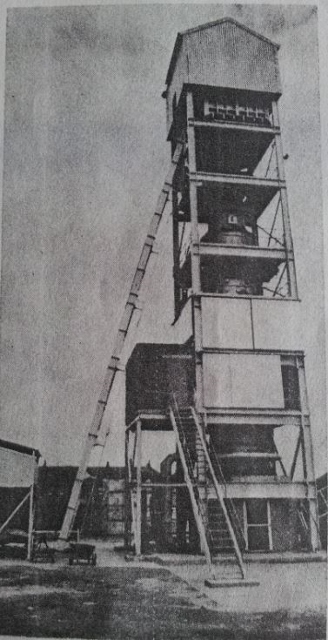