Scottish Brick Company – Following nationalisation of the coal industry in 1947, the National Coal Board (NCB) inherited a number of brickworks. Around 1969, saw the NCB selling off its brickworks with the Scottish Brick Corporation (SBC) taking over most of them, some 33 sites in Scotland. The SBC then started using its own stamp on the bricks it produced, usually the initials SBC. There are various designs of stamp that differ in letter, frog and marks and it is very possible that each site marked their bricks slightly differently in this way.
Scottish Brick Company. Head office in Glasgow and at one time fifteen works in central Scotland producing pressed common bricks. Took over the National Coal Board’s Scottish brickmaking interests in the 1960s (Douglas). The new Centurion plant at Bishopbriggs, producing 72 million facing bricks a year, was opened in 1976. Facing bricks were rarely made in Scotland, the traditional material being stone of roughcast (harling). Carbonaceous shale is mined near the works, crushed, ground, and extruded. The bricks are cut by wires, twenty at a time. There are three kilns each with 28 chambers of 25,000 bricks capacity. (They are of Dutch design, know as Vlammoven, similar to a transverse arch, Staffordshire kiln.) In a normal cycle, 4 chambers are drying, 6 preheating, 5 firing at over 800° C, 5 cooling, one has the top of the wicket open, one has the wicket fully open, and 6 chambers drawing and setting. (Brick and Clay R e c o r d, December 1976).
The following are the SBC brickmarks that I am currently aware of. Please click this link to view them as per the individual posts on my website.
Feb 1969 – NCB and Thomas Tilling group announce a merger of their brickmaking interests in Scotland and the formation of the Scottish Brick Company Ltd with Mr R. W. Parker as chairman.
24/02/1969 – The Glasgow Herald – from 03/02/1969 the NCB and Thomas Tilling merge their brickmaking activities into the Scottish Brick Company.
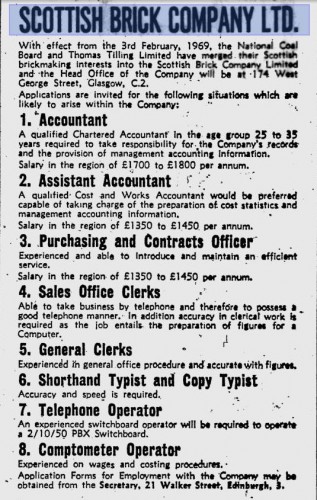
Below – 09/01/1973– The Glasgow Herald – Scottish Brick Company advert – We don’t think that contractors deserve the breaks they get.

Below – 20/02/1973 – The Glasgow Herald – Scottish Brick Company advert – Free area rep with order of bricks! – the classy common brick.
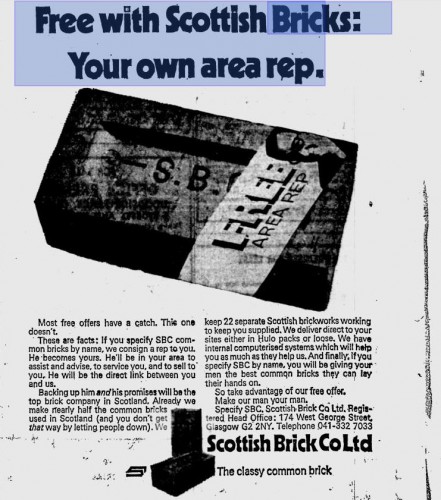
Below – 26/04/1973 – The Glasgow Herald – Scottish Brick Company advert – These letters tell everybody what a fine person you are. The classy common brick.
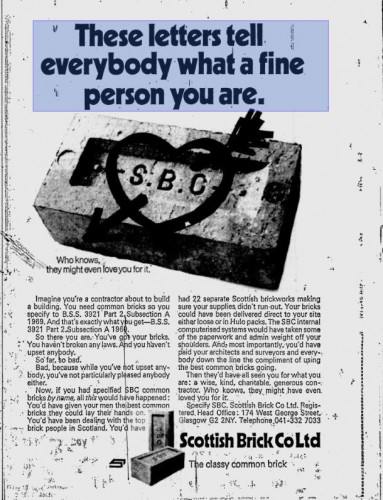
Below – 17/12/1973 – The Glasgow Herald – SBC order 3 x Vlamoven kilns to be built by Gibbons Brothers of Gibbons Dudley Group.

Below – 12/11/1975 – Birmingham Daily Post – SBC require a works engineer for the Centurion Brick Factory North of Glasgow.
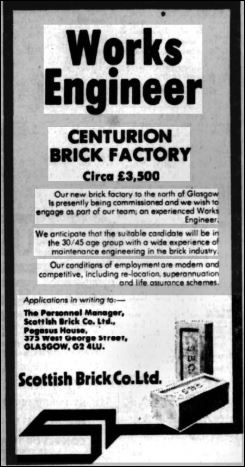
1976 – Brick and Clay Record -Centurion – Face brick in Scotland. New plant for face brick production near Glasgow, Scotland. Three chamber kilns can fire 72 million brick per year. Markets just starting.
Centurion was the name selected by the employees of Scottish Brick Co. Ltd. for the new plant in Bishopbriggs Scotland. Its location near the Antonine Wall, a major Roman civil
engineering project, was the inspiration for this modern face brick plant. Face brick are just beginning to be an accepted building surface in this Central area of Scotland. In the past, brick have been covered with stucco, particularly for home building. The new plant represents a dramatic step forward by Scottish Brick Co. Ltd. to establish this new market.
Mine high carbon shale – High carbon shale is mined near the plant and is stockpiled until needed. A front end loader moves the shale to three hoppers feeding a double roll crusher. Crushed material moves into the feed hopper, then is taken automatically as needed to a system of three grinding mills. Ground shale is conveyed to double shaft pug mill mixer where some moisture is added. One man operates this entire raw material preparation department.
The mix spends at least 20 minutes in a souring tower before feeding out the bottom and moving to the two extrusion lines. Slugs of extruded clay are side cut, 20 at a time, and off-beared into docks on alternate sides for lift truck pick up. Packages of 500 brick are assembled here and taken directly to the kiln. Three chamber kilns, each with 28 compartments, are used to fire the brick. Each compartment holds about 25,000 brick. In a normal cycle, four compartments are drying; six are pre-heat; five are burning more than 800 C.; five are cooling; one has the door top removed, and one has the door open. The other six are working compartments. Burners are on top, firing down the side of the setting. Every 12 hours they are moved forward one complete compartment.
Brick are unloaded by lift truck and banded into a 500 brick package without a pallet.
The Centurion plant is continuing to improve manufacturing technique. Additional clays for body composition are being tested and various surface texturing will be added. As customer acceptance increases and Scottish Brick Co. is convinced that it will, Centurion will be able to meet that demand.
December 1976 – Brick and Clay Record – Scottish Brick Corporation. Head office in Glasgow and at one time fifteen works in central Scotland producing pressed common bricks. They took over the National Coal Board’s Scottish brickmaking interests in the 1960s (Douglas). The new Centurion plant at Bishopbriggs, producing 72 million facing bricks a year, was opened in 1976. Facing bricks were rarely made in Scotland, the traditional material being stone or roughcast (harling). Carbonaceous shale is mined near the works, crushed, ground, and extruded. The bricks are cut by wires, twenty at a time. There are three kilns each with 28 chambers of 25,000 bricks capacity. (They are of a Dutch design, known as Vlammoven, similar to a transverse-arch Staffordshire kiln.) In a normal cycle, 4 chambers are drying, 6 preheating, 5 firing at over 800 0 C, 5 cooling, one has the top of the wicket open, one has the wicket fully open, and 6 chambers drawing and setting.
Below – 21/05/1994 – Newcastle Evening Chronicle – Centurion Scottish Brick, Centurion Works, Old Edinburgh Road, Tannochside, Uddingston G71 7LN – are pleased to be associated with ‘Brick Services’ and wish them every success in the future. (Note – SBH – Brick Services were a company operating out of Patterson Street, Blaydon, Tyne and Wear).
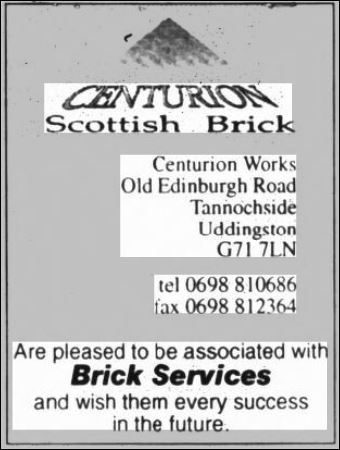
07/04/1995 – Independent – Ibstock purchases Centurion Brick and Scottish Brick in 1995 (Note – SBH – The company then became the Ibstock Scottish Brick Ltd. Tannochside Factory, Old Edinburgh Road, Uddingston, Lanarkshire)
Ibstock, Britain’s third-largest brick manufacturer, confirmed yesterday that it had approached Tarmac with a view to buying its brick-making operations. It said it was too early to say whether a deal, estimated to be worth between £60m and £90m, would go ahead.
Ibstock, which bounced back into the black in the first half of 1994 after two years of heavy losses, said recently it planned to increase its brick-making capacity following the sale of its stake in Caima, a Portuguese forestry and pulp company.
Tarmac, which ranks fourth in the UK after Ibstock, Hanson and Redland, made about 300 million bricks last year, less than 10 per cent of the market. It is understood to have considered that share to be too small to be regarded as a core business.
The acquisition would almost double Ibstock’s market share of about 11 per cent, taking it ahead of Hanson and Redland, which both have just under a fifth each.
It has already increased its capacity by 50 million bricks this year with the purchase for £15m of Centurion Brick and Scottish Brick.
Following a recovery in demand from housebuilders, especially in the first half of last year, the industry is starting to rebuild capacity for the first time since the beginning of the building slump.
Brick sales rose by about 11 per cent last year and further increases are expected this year. Stock levels have fallen sharply, reaching the lowest levels for six years and more capacity is needed even if, as expected, the housing market remains relatively subdued.
Analysts questioned the wisdom of Ibstock swapping one highly cyclical business – pulp – for a focus on another.
Caima, in which Ibstock holds a 56 per cent stake worth just under £50m, suffered heavily in the recession and the closure of one of its plants cost Ibstock an exceptional £18m in 1992.
As with bricks, the industry had become oversupplied and prices for pulp fell from a high of $720 a tonne in 1989 to $350 at the bottom of the cycle.
Despite rises of about 8 per cent in brick prices last year, and more increases forecast for this year, prices remain well below the peak £190 per thousand makers were achieving in 1989.
Since then, however, capacity has fallen by a quarter, with the loss of more than 500 jobs, and last year brick plants were working at full capacity.
2018 – Centurion Brick (Tannochside) Limited is a dormant company incorporated on 8 July 1988 with the registered office located in Livingston, West Lothian. Centurion Brick (Tannochside) Limited has been running for 30 years 6 months. There are currently 2 active directors and 1 active secretary according to the latest confirmation statement submitted on 24th January 2018.
Below are some of the codes as per the Scottish brick Survey published in 1985.
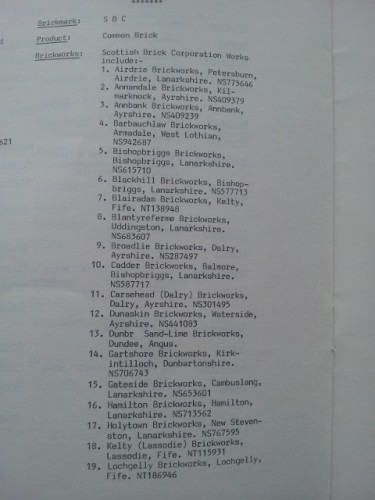
.
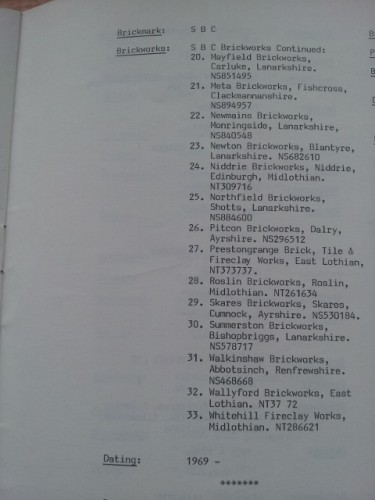
.
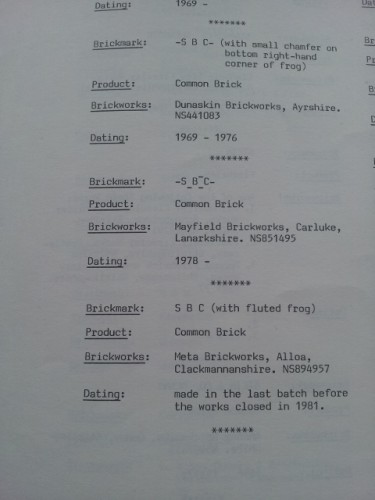
.
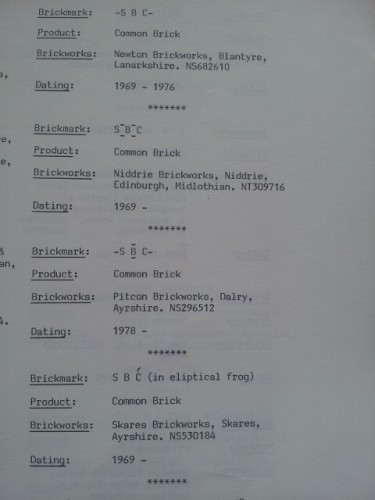
*********************************
Source – Tilcon coloured mortar, brick and block directory 1989
Scottish Brick Corporation Ltd, Centurion Works, Balmuildy Road, Glasgow G23 5HE
Clay bricks.
Multi red, Multi oatmeal, Bute, Antique chocolate – all available in smooth, wirecut and rustic finish.
*******************************