The Falkirk Museum and Archives are in possession of a Bonnybridge Silica and Fireclay Co Ltd brochure.
Unknown date.
It refers to the following brands and brickmarks.
Firebricks – Bonnybridge Brand, BSF – (Semi silica), Calder, Calder L, Calder LS, Octo, Octo M
High Alumina Refractories – Novo 50, Novo 60, Novo 60A, N Sillimanite, Super 70
Refractory jointing materials:-
Bonnybridge dry ground gannister
Bonnybridge dry ground fireclay
Bonsilene
BS Refractory cement No 1
BS Refractory cement No 3
BS Refractory cement No 3M
BS Refractory cement No 7
BS Refractory cement No 7N
Bonsil Brand Refractory Mouldables:-
Bonsil No 2
Bonsil No 4
Bonsil No 5
Bonsil No 7
Boncrete Brand Refractory Castables:-
Boncrete AR1
Boncrete LT
Boncrete No 1
Boncrete No 2
Boncrete No 5
Boncrete No 7
********************************
REFRACTORY JOINTING MATERIALS
BONSILENE
This is a special jointing mixture, extremely fine and of smooth working properties, which has been developed for jointing the brickwork of ladles carrying corrosive slags where thinness of joints is of the utmost importance.
BONSILENE is normally supplied dry but can be supplied blended and ready for use, tempered to a soft plastic consistency under the name BONSILENE PLASTIC.
B.S. REFRACTORY CEMENT No. 1 Designed as a suitable jointing cement for use with BONNYBRIDGE, B.S.F., and CALDER brands. This cement is of very fine texture, is air-setting and contains the minimum of ingredients which cause shrinkage on drying and firing.
********************************
REFRACTORY CASTABLES
BONCRETE No. 2
This refractory concrete is somewhat harsh in working and must be rammed or vibrated into position. Very thorough mixing with the correct amount of water (not more than 1 ½ gallons per cwt. Or 7 litres per 50 Kg.) followed by curing accordingly to the directions given, is necessary for the best results. Suitable for conditions where abrasion is not severe, and temperatures up to 1400 C.
BONCRETE No. 5
This is a specialised refractory concrete (alumina content 57%) with excellent strength throughout the temperature range from atmospheric to 1500 C. Rapid placement, with vibration, advised for the best results.
BONCRETE No. 7
A super-refractory castable (alumina content over 75%) capable of the highest heat duty. Recommended for conditions demanding stability up to 1700 C.
************************************
REFRACTORY JOINTING MATERIALS
B.S. REFRACTORY CEMENT No. 3
This highly refractory jointing cement is recommended for use with our OCTO and NOVO 50 brands. It has a refractoriness of Cone 34 (1750 C) is air-setting and has negligible shrinkage on drying and slight expansion on firing. A protective layer of a wash of B.S. CEMENT No. 3 will be found useful in fortifying porous refractories, including high temperatures insulation, against slag attack and erosion.
B.S. REFRACTORY CEMENT No.3M
This cement has been developed especially for use with our OCTO M Blast Furnace Stack brick. It is of substantially the same fired analysis as OCTO M bricks and is extremely finely ground to ensure thin joints. B.S. CEMENT No. 3M is highly workable yet free from drying and firing shrinkage: for Blast Furnace work we recommend that no cold setting agency be used, and the cement as normally supplied is heat setting. Cold setting properties can be incorporated to special order.
B.S. REFRACTORY CEMENT No.7
This highly refractory cement (Cone 36) is manufactured specifically for use with NOVO SILLIMANITE bricks.
B.S. REFRACTORY CEMENT No. 7N
A less costly variation of B.S. CEMENT No 7 this cement has been developed for use with our NOVO 60, 60A and SUPER 70 brands. The above cements have negligible shrinkage on drying and are slightly expansile at operating temperatures. They can be supplied with or without air-setting properties.
*******************************
REFRACTORY MOULDABLES
BONSIL BRAND
These versatile materials, sometimes known as “Plastic Refractories”, can be used to form jointless or monolithic furnace linings. This is done by ramming, pounding or trowelling: grades are supplied suitable for each method of application. All the BONSIL grades contain a very high proportion of highly calcined refractory aggregate bonded by a special process which imparts workability without loss of refractoriness. Strength is attained without the use of fusible bonding ingredients which would be destroyed on heating. Correctly applied, BONSILS show negligible drying shrinkage. Firing shrinkage, where not entirely absent, can also be disregarded. For patching and repairs (cold or hot), the substitution of intricate special shapes, general jointless construction with a measure of thermal insulation and for reasons of convenience and availability. BONSIL REFRACTORY MOULDABLES merit the consideration of all responsible for furnace construction and maintenance
DIRECTIONS FOR USE
Mix the whole contents of one drum or bag to ensure uniform moisture distribution. Avoid contamination with other cements, mortars, or other materials ALWAYS WORK BONSIL AS STIFF AS POSSIBLE-the less water it contains at the time of application, the less will be the DRYING SHRINKAGE.
If applied by the RAMMING or TAMPING method, its consistency should be such that it will just stick together if gripped tightly in the hand: drying shrinkage is then negligible. To apply in the soft-plastic state, e.g., by trowelling, pure water should be added until the mixture has the desired consistency.
THE SURFACE to be PATCHED or REPAIRED should be free from dust, slag or vitrified brickwork. Smooth surfaces should be roughened by chipping or scoring before applying BONSIL.
For EXTENSIVE PATCHES, especially if more than three inches thick, some means for high-temperature linings. CALDER or OCTO firebricks built into and protruding from the wall behind provides safe support.
THICK LININGS should always be made by RAMMING or TAMPING, and for this purpose, it is advisable to confine the shape to be moulded in a strong frame of wood or other material. In overhanging positions, the support should be left in place until the BONSIL has become firm.
TAMP LAYERS about 2 in. (5cm.) thick-roughen the surface of each layer before proceeding with the next.
SPECIAL SHAPES can be made by moulding or ramming BONSIL either in situ or with independent moulds. At stiff consistency, drying shrinkage is less than 1 per cent, and for most purposes can be neglected.
DRYING can be very rapid, especially with thin patches of low moisture content. The thicker and wetter the monolithic section is, the more cautiously it must be dried. Vent holes for the escape of steam may be provided with advantage.
FIRING. Full strength will be developed at the full heat of the furnace and until this has been reached mechanical damage to the lining should be avoided.
RETURN UNUSED BONSIL to drum, cover with wet sacking and replace lid tightly. Should the material become dry or hard, it can be restored to full workability by the addition of water.
*********************************
REFRACTORY MOULDABLES
BONSIL No. 2
This is a smooth refractory putty, of medium refractoriness (Cone 29). It has air-hardening properties and may be used for the union of refractory with metal. Amongst other applications, it is used successfully for patching coke oven doors and jambs. Supplied in air-tight drums ready for immediate use.
BONSIL No. 4
Refractoriness cone 32. This medium-priced plastic patching material gives excellent service where moderate conditions are encountered. Such applications include ceramic kilns, furnace walls and burner parts where operating temperatures are in the region of 1250-1300 C. It has also been used most successfully as a monolithic ladle lining. Supplied semi-dry in bags, or plastic, ready for trowelling in air-tight drums.
BONSIL No. 3
Contains a highly refractory aggregate, and after firing becomes the equivalent of a super duty firebrick. E.g., our OCTO Brand, of refractoriness Cone 34. It has also the important and valuable property of remaining constant in volume after firing to temperatures as high as 1450C. This freedom from the common fault of shrinkage at high temperatures occasions no loss of thermal shock resistance, and also makes it extremely useful in such applications as electric furnace crowns.
BONSIL No. 7
This material has been produced for use where extremely severe operating conditions are experienced. Containing a sillimanite type aggregate, it produces a monolithic refractory of 58% AI O and refractoriness Cone 36 (1790 C) Like other products in this range it is volume stable under operating conditions and is particularly suitable for burner ports, crucible furnaces and applications where a large safety factor is required.
*********************************
REFRACTORY CASTABLES
BONCRETE BRAND
The BONCRETES have all the well-known advantages of concretes, the monoliths produced from them having also the properties of conventional refractories. All content of graded refractory aggregates mixed with refractory cements are supplied dry and are applied in a manner rather similar to conventional concrete practice, subject so important refinements set out below. The cast monoliths so made have excellent spalling resistance, good thermal insulation and many other valuable properties.
DIRECTIONS FOR USE
Mixing
The whole contents of each container (bag or drum) must first be mixed dry. Any unwanted mixture can then be returned to the container for later use. The mixture required is then placed in a watertight container, soaked with the requisite water and allowed to remain soaking for about half an hour. This must not be greatly exceeded. The moist mixture is once more thoroughly mixed before placing. Best results are obtained by the use of mixtures too dry to pour, which are consolidated by vibration or other means.
Curing
It is important to prevent the escape of moisture from the cast unit for 16-20 hours after mixing. This may be done by total immersion in water or by confining the shape completely within waterproof material, e.g., tarred paper. Properly prepared refractory concrete generates a good deal of heat during the first day and escape of water due to this should be prevented. Refractory concrete starts to set within three hours after initial mixing with water, has strength enough to permit removal of moulds, if desired, after about 5 hours (earlier if rammed semi-dry) and great strength after 24 hours. Every effort should be made to cast large units in quickly successive batches as it is a matter of difficulty to secure satisfactory union between batches placed at time intervals of an hour or more. Refractory concrete is ready for service after 24 hours proper curing but gains gradually in strength if left under atmospheric conditions for longer periods.
Drying and preheating
It is advisable to limit the rate of the rise of temperature of fresh refractory concrete to 50 C per hour until the whole mass exceeds 600 C, because of the considerable evolution of steam. Above 600 C and from cold on all subsequent occasions, the mass can be heated at any practical rate without damage. Refractory concrete intended to carry heavy loads at high temperatures benefits by being first dried and fired without load.
Reinforcement
As an ordinary concrete engineering practice, reinforcement of refractory concrete may be beneficial, especially in massive overhanging units. The design and choice of metallic or refractory brick reinforcement should be discussed with our Technical Department.
*****************************
BONCRETE AR1
A high strength abrasion resistant concrete, suitable for use up to 1100 C, valuable for furnace shop floors where metal and slag spillage may occur and in similar applications.
BONCRETE LT
Low-cost refractory concrete, relatively slow setting but with very high ultimate strength, recommended for use up to 1000 C, Semi-dry placement with vibration, advised for best results.
BONCRETE No 1
This is a fairly “rich” mixture, suitable for general purposes where high strength is important and where temperatures will not exceed 1200 C. The amount of mixing water required is 2 ½ gallons per cwt. (10 litres per 50 Kg.) or rather less if vibration-placing can be used.
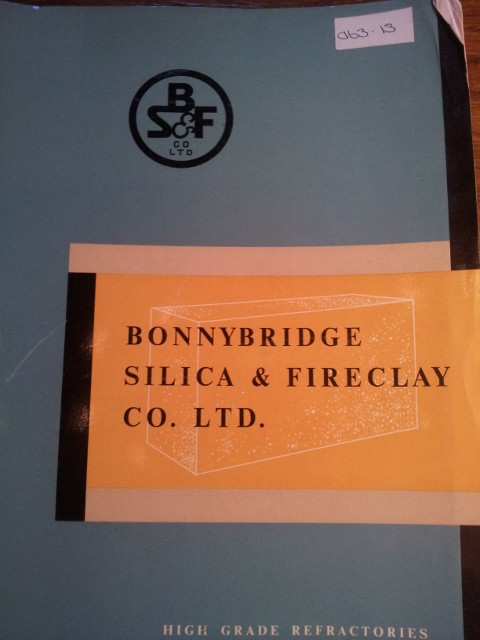