Found at the Stein Manuel Works, Whitecross.
Ron Toothill identifies this as a SULB brick. He states – SULB bricks “Semi-Universal Ladle Brick” would only be used on the working lining only and designed to speed up the bricking of steel ladles. They would be placed end to end onto two specially designed refractory ramps. Two bricklayers would work at 180 deg to each other in the ladle. Because they were radiused, a large number of ever-increasing diameters could be met. Once bricking has been completed towards the top of the ladle, then either a pre-fabricated closing refractory brick ramp would be used on either side of the ladle or perhaps simply finished off using a refractory concrete to close the ladle top. Steel ladles are good business for refractory manufacturers because they only have short working lives and need replacing often. We would manufacture the high alumina SULB’s at GR Stein Manuel works, both as a 76mm thick brick for the American market and also a 100 mm thick SULB for the rest of the world. Possibly a Stein 45 for the European market because of the 100mm depth.
Insulation lining – both Iron and Steel ladles have an insulation layer of either a refractory concrete or insulation bricks placed next to the shell. These don’t need much maintenance and don’t often get removed when re-bricking a ladle. When insulation bricks are used, two different size arch taper bricks are used.
Example – because the ladle is not vertical every ring of bricks has a slightly different ideal taper.
The outside diameter of brickwork 3000mm
Lining thickness 76mm
Back of the side arch brick measures 114mm.
Inside diameter of brickwork 2848
The ideal taper is 108.2mm
3000/2848 x 114 = 108.2.
Therefore if we manufactured a brick to suit this particular outside diameter of 3000, then we would need to make it 230 x 114/108.6 x 76mm. Now as you can imagine, every other brick course either below or higher than this particular course would be a slightly different diameter and therefore require a slightly different brick, because the ladle slopes a little and is not vertical.
Consequently, when designing the brickwork for the ladle we would need to find the ideal taper for both bottom and top course using the above maths first.
Example – top course outside diameter – 3200mm = 108.6mm ideal taper.
bottom outside course diameter -2750mm = 107.7mm ideal taper
Instead of making lots of slightly different sized taper bricks to suit different diameters, we would mix two different manufacturing standard Side Arch bricks together. We would probably use say a 114/110 and a 114/105. Because one brick is slower 114/110 and the other is sharper 114/105 than the both ideal tapers required. These two standard bricks used together in different ratios would brick all of the courses between the top and bottom of the ladle. Sometimes if the ladle is so high and the slope is steep then we would use three different standard bricks to brick the ladle. Using very sharp and very slow bricks together can cause other problems when bricking. That is why we would use three different standard side arch bricks on steep sloping ladles.
SULB courses – occasionally working lining SULB bricks are used without the use of starter and finishing ramps. When this is the case the use hydraulic rams may be used again before measuring the closing gap. Two SULB bricks are then cut with radial cuts to enable them to be placed next to each other in the gap. I have always thought that using SULB bricks with starter and finishing ramps must be quite loose as opposed to closing courses with bricks cut to suit the remaining gap. In reality, though this has never been a problem apparently.
How was the brick secured to the metal ladle? – Okay side arch bricks, after bricking say 350 deg of any course, we would then measure the horizontal distance between the first and last brick (10 deg gap}. To secure this course of brickwork and the gap is now less than less than 114mm, we need then to cut some bricks vertically, either two or three depending upon the size of the gap. But be sure not to cut a brick less than 50mm thick. On working linings, but not insulating (soft) bricks, the use of horizontal hydraulic rams can be used to gently push the last and first bricks apart to tighten up the course before measuring the gap.
Below – This SULB measures 20.7 cm long at top of the curve.
18.7cm long at bottom of the curve.
15 cm wide
10cm deep
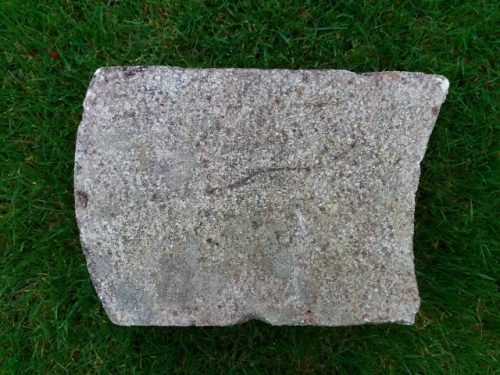
.
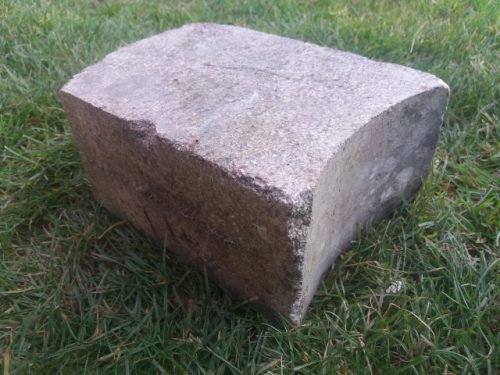
Below – Some relevant information. Harbison-Walker.
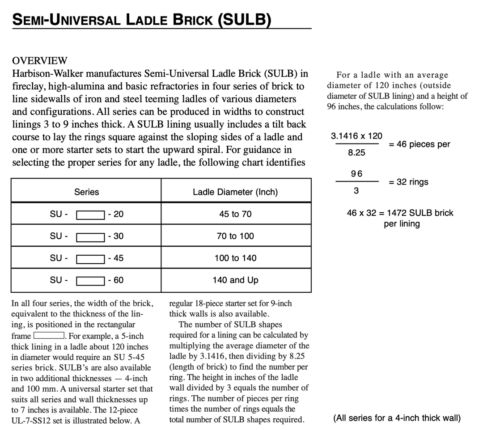
.
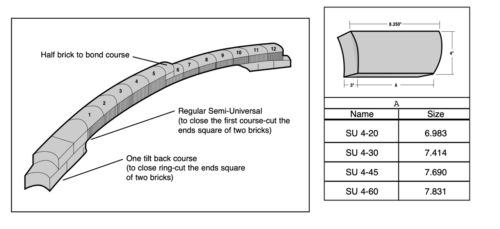
Patent – This is a link to a patent for ladle starter shapes. Ladles were often constructed by laying bricks in a spiral so the bottom and top courses would need to be completed using a series of special shapes.
“The invention consists of a universal set of refractory starter shapes having a combination of universal shapes in semi-universal shapes juxtaposed in such a manner as to form a starter course for constructing helical (corkscrew or spiral) linings in ladles of varying diameters”.