This page is a compilation of adverts relating to John Gilchrist Stein. Many thanks to Graham Brooks for the ‘Bulletin of the Institution of Mining and Metallurgy’ references.
Below – 1930? – John G Stein advert.

Below – 1933 – John G Stein advert.

Below – 1938 – John G Stein advert.

Below – 1938 – Scottish EXH Magazine
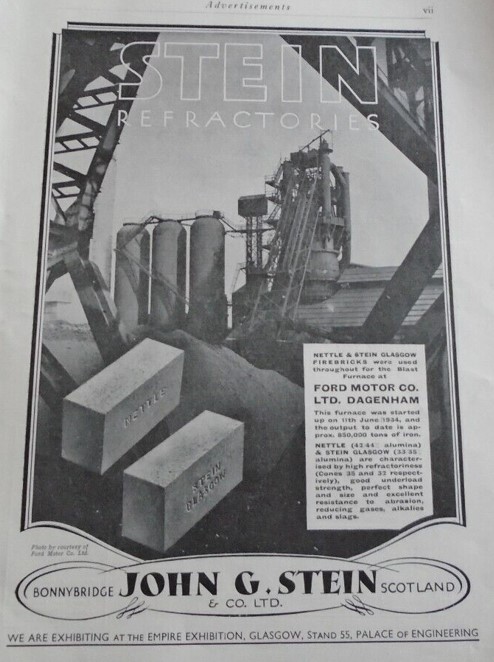
Below – 1940 – John G Stein advert.
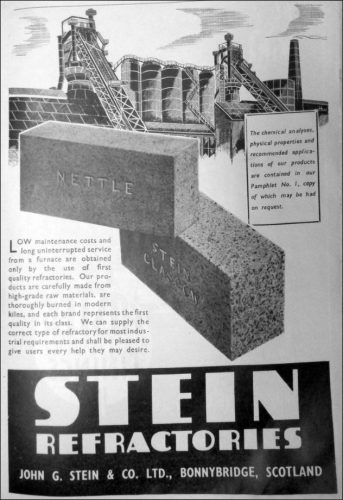
Below – June 1941 – Bulletin of the Institution of Mining and Metallurgy – Stein Refractories. Stein Chrome, Stein Dikro, Stein KM, Stein Mag, Stein Dimag.
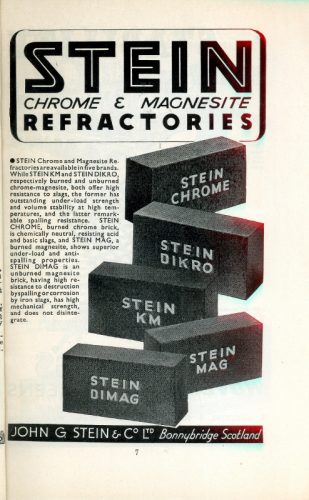
Below – March 1946 – Bulletin of the Institution of Mining and Metallurgy – Stein Refractories.

Below – August 1947 – Bulletin of the Institution of Mining and Metallurgy – Stein Refractories.
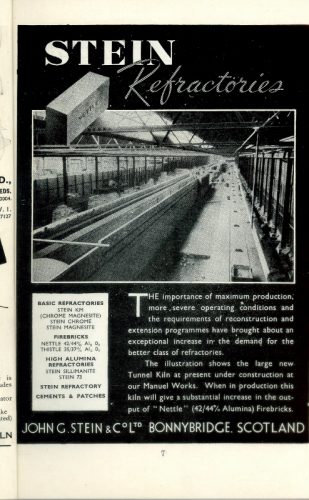
Below – October 1947 – Bulletin of the Institution of Mining and Metallurgy – Stein Refractories.

Below – August 1948 – Bulletin of the Institution of Mining and Metallurgy – Stein Refractories.
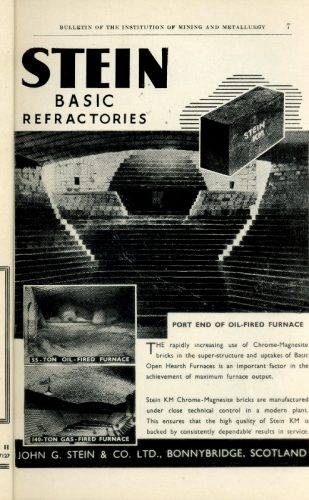
Below – October 1948 – Bulletin of the Institution of Mining and Metallurgy – Stein Refractories.
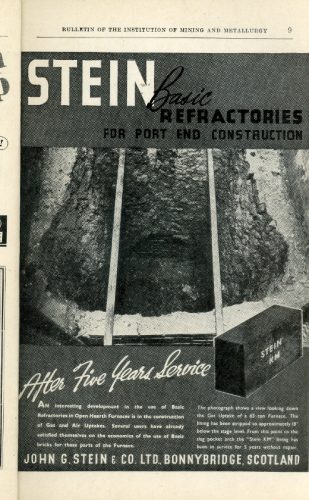
Below – 1951 – John G Stein advert.

Below – February 1952 – Bulletin of the Institution of Mining and Metallurgy – Stein Refractories.

Below – 1960 – John G Stein advert.
Firebricks
Nettle – 42 % alumina
Thistle – 33 – 35 % alumina
High Alumina Bricks
Stein 50
Stein 63
Stein 70
Stein 73
( Stein 80 – see 1938 advert below )
Stein Sillimanite
Stein Mullite
Basic Bricks
Stein Magnesite
Stein Mag
C Stein Dimag
Stein KM
Stein Dikro
Stein Chrome

Below – Unknown date – John G Stein advert.
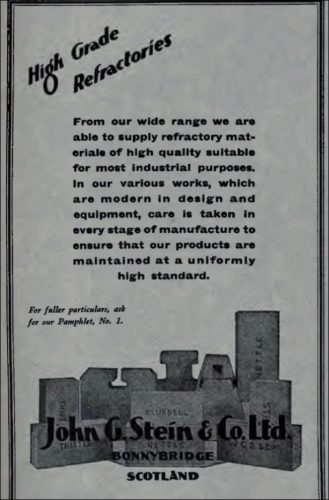
Below – Unknown date – John G Stein advert.
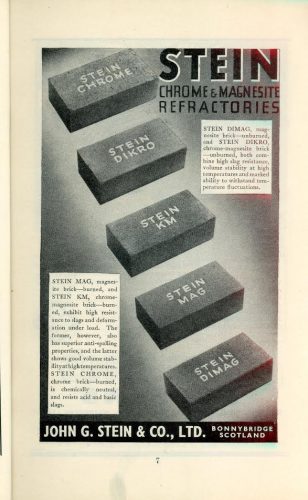
Below – date unknown.
High alumina bricks – in the last few years high alumina bricks – especially those above 60% alumina and over – have definitely established themselves in positions where combined resistance to load, corrosion and spalling is required. Bricks of this group are represented by
Stein Sillimanite 63% alumina
Stein 63 – 63% alumina
Stein 80 – 80% alumina
Their principal features are –
- High refractoriness
- Excellent resistance to basic slags
- Excellent load-bearing properties at high temperatures
- Constancy of volume
Insulating Refractories
A special development in furnace constructional materials has been the production of refractories which have low heat flow, small heat capacity and lightness in weight. “Stein H.T.I” combines the properties of an effective insulator with those of a firebrick. It is highly refractory, possesses good mechanical strength and can be used in positions directly exposed to the heat up to 1450c where slagging and abrasion are absent or unimportant.
Because of its low thermal conductivity and heat capacity (both approx 1/4 of ordinary firebricks) the use of “Stein H.T.I” cuts down the size and weight of a furnace and reduces considerably the heat locked up in the structure. In intermittently working furnaces that is particularly important and means considerable saving in the time required for heating up and in fuel.
Silica Bricks
96% silica refractories represented by our Bluebell and Myrtle brands are the important materials of construction in many metallurgical and carbonising furnaces. The use of high silica material is due to its retention of strength and rigidity right up to a very high temperature eg 1600 – 1650C.
In comparison, fireclay refractories show definite plastic deformation at relatively low temperatures, ranging from 1200c to 1450c, depending on quality.
It follows, therefore that the use of 96% silica with its high load-bearing characteristics has proved of enormous importance in furnace construction and economy.
In order to exhibit their high resistance to load, silica bricks have to be burned for a long time at a high temperature. This results in the complete conversion of the original quartz wither to cristobalite or to a mixture of cristobalite plus tridymite or to Tridymite alone.
Cristobalite and Tridymite have excellent high-temperature properties, but at low temperatures – 200 – 300c – they have a marked reversible volume change. Heating or cooling through this temperature range, therefore, must be done slowly and carefully, otherwise, the bricks are easily cracked and disrupted.
The important uses of 96% silica bricks for the iron and steel industry are:-
Open hearth furnace – Crown and Linings
Regenerator – Linings and Fillings
Bessemer Converters
Electric Furnaces
Coke Ovens